How to Calculate Air Flow in a Pipe
Air flow differs from water flow in that air is compressible and water is not.
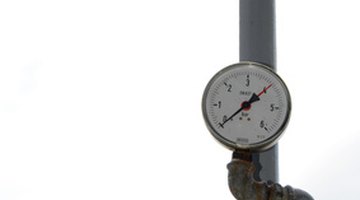
The result is that calculating either volumetric or mass water flow rates are straightforward, while the volume of a given mass of air may change significantly based on the temperature and pressure changes that take place in the measurement process. Calculating standardized or mass-related volumetric air flow in a pipe may require correction for "before and after" pressure and temperature conditions around the flow-sensing element. These corrections take place under the square root radical.
Tip
Moving up one size pipe adds to flowing efficiency over the long term.
Warning
Compressed air should always be put through steel pipe or approved plastic pipe only, as some plastic pipes will shatter and let pieces fly.
-
Define the air flow application. In this case, 135-pound-per-square-inch (psi) compressed air is being conveyed through a three-inch Schedule 40 steel pipe to a treatment facility 350 feet away. The pressure gauge at the end of the pipe reads 112 psi. With this information you can calculate the air flow through the three-inch pipe.
-
Calculate 5 percent of 135-psi, which would be a maximum recommended pressure loss per 100 feet of pipe at 135 psi to still be energy-efficient. Substituting values, 0.05 X 135 = 6.75 psi.
-
Calculate the pressure loss per 100 feet of pipe, since this is how published pipe flow data is presented. 135 psi minus 112-psi = 23-psi/350/100 = 6.57-psi drop per 100-feet. As 6.57 psi is less than 6.75 psi, this example lies in the "efficient" realm.
-
Look up the flow data for 135 psi compressed air in three-inch pipe. Since there is only data for 100 psi and 150 psi, you can correct from either point for both drop and static pressure and compare.
-
Correct from the 100 psi point by interpolating drop and correcting for static pressure. The flow data would be 2600 SCFM (Standard Cubic Feet per Minute) with a pressure drop of 5 psi (5 percent of 100 psi). The air flow at 135 psi = 6.57 psi drop/5 psi drop X 135 psi/100 psi = 1.7739. Extracting the square root of 1.7739 yields 1.3318. Multiplying the 1.3318 by 2600/SCFM yields 3462 SCFM.
-
Correct from the 150 psi point. The flow data is 3900 SCFM with a pressure drop of 7.5 psi. The air flow at 135 psi = 6.57 psi drop/7.5psi drop X 135 psi/150 psi = 0.7884. Extracting the square root yields 0.8879. Multiplying the 0.8879 X 3900 SCFM yields 3462.88 SCFM.
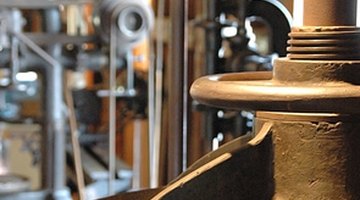
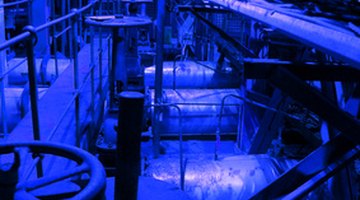
The Drip Cap
- Air flow differs from water flow in that air is compressible and water is not.
- These corrections take place under the square root radical.
- Calculate 5 percent of 135-psi, which would be a maximum recommended pressure loss per 100 feet of pipe at 135 psi to still be energy-efficient.
- The air flow at 135 psi = 6.57 psi drop/5 psi drop X 135 psi/100 psi = 1.7739.
- Multiplying the 1.3318 by 2600/SCFM yields 3462 SCFM.
- Correct from the 150 psi point.
References
Resources
Writer Bio
Pauline Gill is a retired teacher with more than 25 years of experience teaching English to high school students. She holds a bachelor's degree in language arts and a Master of Education degree. Gill is also an award-winning fiction author.
Photo Credits
- gauge image by DXfoto.com from Fotolia.com
- gauge image by DXfoto.com from Fotolia.com
- Industrie image by Carsten Steps from Fotolia.com
- Steam Pipes image by Andrei Merkulov from Fotolia.com
More Articles