How Is Plexiglass Produced?
Plexiglass is the original trademark name for transparent acrylic plastic sheets of poly(methyl methacrylate), or PMMA. The most popular production technique for PMMA is known as the ACH, or acetone cyanohydrin, route.
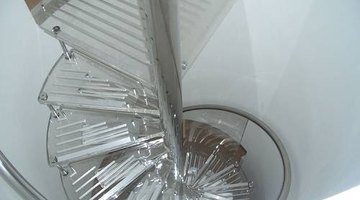
The ACH Route
The ACH route is used to create methyl methacrylate, a derivative of methacrylic acid and the basis of acrylic plastics such as PMMA. First, acetone cyanohydrin is created in a chemical reaction between acetone [CH3COCH3] with sodium cyanide [NaCN]. The acetone cyanohydrins created in this process is then reacted with methyl alcohol [CH3OH] to create methyl methacrylate [CH2=C(CH3)COOCH3]. The equal sign signifies the double covalent bond between carbon atoms of the methyl methacrylate monomer. This double covalent bond is broken during the polymerization process that creates the basic material of Plexiglass.
Polymerizing MMA
After the methyl methacrylate (MMA) has been created from the ACH route, the monomers, or chemical molecules, of the substance are isolated for the polymerization process. Methyl methacrylate is poured into a mold with an appropriate catalyst which breaks the double covalent bond of the MMA. The monomers begin polymerizing in the mold as broken covalent bonds begin joining other broken covalent bonds, creating poly(methyl methacrylate).
Batch Cell Bulk Polymerization
Batch cell bulk polymerization is a popular industrial polymerization process for making thicker sheets of PMMA. The MMA and catalyst are poured into a mold made of glass or metal plates laid on top of each other, connected by a spacer. Sometimes, a prepolymer solution of partially formed methyl methacrylate polymers is added to aid the reaction. As the liquid solution is poured into the batch cell mold, the spacer expands the glass or metal plates expand to accommodate the liquid. The mold is sealed, and heat is applied to induce the reaction to start. After the reaction has begun, the heat is removed and the excess heat generated by the reaction is allowed to vent. As the PMMA cools and hardens, it will contract. The spacer allows the plates to contract as the PMMA's form contracts, keeping the acrylic sheet level. The entire process can take anywhere from 12 hours to several days depending on the sheet's thickness. After the sheet cools, it can be annealed, or heat treated to prevent brittleness, at temperatures of 150 degrees Celsius.
Uses of PMMA
Poly(methyl methacrylate) has a multitude of uses. PMMA gained its popularity during World War II as a durable substitute for glass, but today it can be found in headlights, acrylic mirrors, medical implants and even musical instruments. Depending on what the PMMA will be developed for, the polymerization process will differ greatly for proper shaping and treatment. The basic batch cell bulk polymerization process creates the acrylic sheets that many people refer to as Plexiglass. Different processes are used to create the PMMA that goes into bone cement used by orthopedics to secure bone implants in patients. PMMA has also been developed to create a tattoo ink called Chameleon Tattoo Ink which causes a tattoo to glow under blacklight exposure.
References
Resources
Photo Credits
- Photo by David Bolton (License: Creative Commons Attribution)
- Photo by David Bolton (License: Creative Commons Attribution)
More Articles