The Differences Between Drawn & Extruded Aluminum
Aluminum is an extremely versatile material used in a wide range of products from hardware to soda cans. There are many different ways to shape aluminum, but all of them involve using some sort of die or mold. Drawn and extruded aluminum are the two primary types of aluminum production.
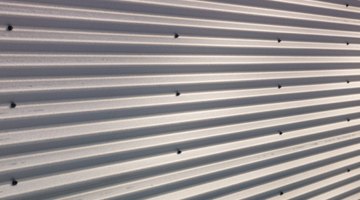
With both methods, the aluminum is first formed into a billet, or long tube, then cut to the specific length, depending on the product.
Extruded Aluminum
Extruded aluminum is made by heating the aluminum and forcing it through a die. What comes out on the other side is the shape of the final product. To visualize the process, imagine pushing a ball of clay through a circle punched with holes. What comes out on the other side is a series of spaghetti-like strands. The shape of the die determines what the final product will look like. For example, an āIā shaped die creates aluminum I-beams. After the product comes out of the die, it is cooled and then stretched to remove any twisting that occurs during the cooling process. As it hardens, extruded aluminum becomes stronger. The hardening process can take place at room temperature, but since that can be time consuming, most manufacturers employ heated rooms to temper the aluminum quickly.
Extruded Aluminum Tubing
There are two types of structural tubing made by the extrusion process. In the first one, the aluminum tube is split and then resealed using high temperature, pressure and metallurgical welds. The seam created during this process is sometimes visible to the naked eye. Tubing made this way is not suitable for transporting gases or liquids under extreme pressure as there is a risk of the seam splitting. In the second process, the tube is produced by pushing a hollow billet through a die. Because this tube does not have a seam, it can safely be used to transport or store pressurized gases and liquids.
Drawn Aluminum
The main difference between extruded and drawn aluminum is the way the aluminum is shaped by the die. While extruded aluminum is pushed through a die to obtain its desired shape, drawn aluminum is pushed into a mold. The aluminum is stretched out into the mold, undergoing what is called plastic deformation. Determining the flexibility of the aluminum, or its plasticity, is a critical part of the process because the aluminum cannot be stretched to the point where it becomes brittle or tears. Drawn aluminum typically makes cans, pots and other circular objects.
Drawn Structural Tubing
In the beginning, a drawn structural tube goes through the same process as an extruded tube. However, where an extruded tube is cooled after it is forced through the die, the drawn tube is sent through a second die. This process is called cold drawing or cold working, and it is here that the final dimensions of the product are determined. A drawn tube is just as suitable for transporting gases or liquids under pressure as a seamless extruded tube.
The Drip Cap
- Aluminum is an extremely versatile material used in a wide range of products from hardware to soda cans.
- What comes out on the other side is the shape of the final product.
- The hardening process can take place at room temperature, but since that can be time consuming, most manufacturers employ heated rooms to temper the aluminum quickly.
- In the first one, the aluminum tube is split and then resealed using high temperature, pressure and metallurgical welds.
- Drawn aluminum typically makes cans, pots and other circular objects.
- In the beginning, a drawn structural tube goes through the same process as an extruded tube.
References
Writer Bio
Bjorck DiMarco has been the Senior Editor at an independent publishing house since 1994. She holds advanced degrees in teaching, English and creative writing, graduating summa cum laude from Tufts University and the University of Massachusetts. DiMarco has also worked in construction, fine woodworking, graphic design and theoretical mathematics.
Photo Credits
- Jupiterimages/Photos.com/Getty Images
- Jupiterimages/Photos.com/Getty Images
More Articles