How to Heat Treat A-2 Tool Steel
AISI A2 tool steel is high-carbon, high alloy tool steel designed to have excellent wear resistance and toughness. The steel is composted of 1 percent carbon, .3 percent silicon, .6 percent manganese, 5.3 percent chromium, 1.1 percent molybdenum and .2 percent vanadium. The prefix "A"
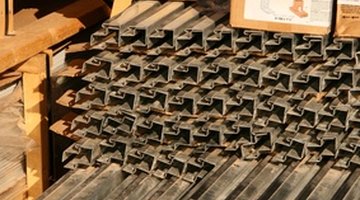
in the name designates it as an air-hardening steel. This means it hardens rapidly compared to other tool steels, making heat treatment potentially difficult.
Things You Will Need
- Forge
- Darkened room
- High-heat thermometer
- Oil
- Bucket
- Protective gear
Tip
An infrared thermometer (relatively low cost) can give precise temperature readings.
Warning
The steel will be extremely hot. Proper protective equipment such as glasses, apron and gloves is crucial.
Heat Treating
-
Heat the steel through to 1,560 degree Fahrenheit using a forge or heat-treat oven . Once thoroughly heated, slowly cool in the furnace by dropping the temperature 20 degrees per hour to 1,200 degrees. This relieves any stress within the steel.
-
Heat the steel slowly over a 15-minute period to the critical temperature, the point where the steel becomes nonmagnetic. For A2, the critical temperature is about 1,575 degrees Fahrenheit, and the steel should have a bright, light cherry-red color.
-
Hold the steel at the critical temperature for 3 to 5 minutes. This period of time is known as the soak time and gives the steel a chance to obtain a uniform temperature.
-
Remove the steel from the forge and quench in oil. It is important to keep the steel moving in the oil since a vapor barrier can form around the steel if left still, preventing the steel from obtaining a uniform heat.
-
Temper the steel according to the intended use. For A2, the most common tempering temperature is 300 to 800 degrees Fahrenheit. Once the steel has reached the intended temperature, hold the steel at that temperature for two hours and let it cool in the air.
The Drip Cap
- AISI A2 tool steel is high-carbon, high alloy tool steel designed to have excellent wear resistance and toughness.
- Once thoroughly heated, slowly cool in the furnace by dropping the temperature 20 degrees per hour to 1,200 degrees.
- This relieves any stress within the steel.
- It is important to keep the steel moving in the oil since a vapor barrier can form around the steel if left still, preventing the steel from obtaining a uniform heat.
References
Resources
Writer Bio
Writer, photographer and world traveler James Croxon is a jack of all trades. He began writing in 1998 for the University of Michigan's "The Michigan Times." His work has appeared in the "Toronto Sun" and on defenselink.com and globalsecurity.org. Croxon has a bachelor's degree in English from the American Military University.
Photo Credits
- steel,construction image by Greg Pickens from Fotolia.com
- steel,construction image by Greg Pickens from Fotolia.com
More Articles