How to Estimate Tuck-pointing Jobs
According to the Masonry Advisory Council, brick has a useful lifespan that can exceed 100 years, but the mortar joints that hold bricks in place have a useful lifespan of only about 25 years. The more mortar joints deteriorate, the greater the chance for potentially damaging water penetration.
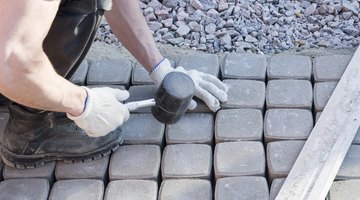
Tuck-pointing is a method for repairing defective joints, but because the process is labor intensive and every job is different, there is no standard cost per square foot. Instead, most contractors will submit a time and materials estimate.
Determine Repair Requirements
Inspect and lightly scrape mortar joints with a metal tool to identify areas that require tuck-pointing. Note areas where there are cracks between the mortar and brick, where mortar is crumbling or has hairline cracks and where you see mortar erosion more than 1/4 inch. According to the MAC, this step is critical, not only because tuck-pointing can be expensive, but also because original mortar joints in good condition are preferred over tuck-pointed mortar joints.
Time and Materials Variables
With tuck-pointing jobs, most of the costs involve labor and setup. If the job is in a location without easy access, it will generally take more time, labor and equipment. A job in progress may also incur additional costs for services such as restoration cleaning or repairing damaged bricks once it gets underway. Unlike a fixed-fee estimate that quotes a specific amount, a time and materials bid identifies the worker’s hourly rate and the cost of materials -- including a profit margin -- based on an initial determination, but leaves the door open for additional charges.
Identify Parameters
Describe job details in the first section of a time and materials estimate. Start with quantity information, including the size of each damaged joint and total linear feet, the size and job titles for each crew member, an estimate for the linear feet the crew can tuck-point in an average work day and the estimated duration of the project. Finally, identify any special equipment, such as a lift truck, that must be rented to complete the project.
Cost Breakdown and Unit Itemizations
The body of the estimate contains labor, materials and equipment cost breakdown information. For each area, specify the quantity, the unit of measurement, such as hours, weeks or bags of mortar, the unit cost and the total cost. Add the totals for each cost breakdown category and calculate the percentage each contributes to the total estimate. Finish by adding in the cost for office overhead and the profit margin to create a grand total.
The Drip Cap
- According to the Masonry Advisory Council, brick has a useful lifespan that can exceed 100 years, but the mortar joints that hold bricks in place have a useful lifespan of only about 25 years.
- Tuck-pointing is a method for repairing defective joints, but because the process is labor intensive and every job is different, there is no standard cost per square foot.
- Instead, most contractors will submit a time and materials estimate.
- For each area, specify the quantity, the unit of measurement, such as hours, weeks or bags of mortar, the unit cost and the total cost.
References
- Masonry Advisory Council: Repointing (Tuckpointing) Brick Masonry
- ATEK Tuckpointing: How Much Does Tuckpointing Cost?
- Panoptic Development: Why Billing on a Time and Materials Basis Really Is Customer Friendly
- The American Society of Professional Estimators: How to Estimate the Cost of Masonry Tuckpointing
Writer Bio
Based in Green Bay, Wisc., Jackie Lohrey has been writing professionally since 2009. In addition to writing web content and training manuals for small business clients and nonprofit organizations, including ERA Realtors and the Bay Area Humane Society, Lohrey also works as a finance data analyst for a global business outsourcing company.
Photo Credits
- K-Paul/iStock/Getty Images
- K-Paul/iStock/Getty Images
More Articles