Advantages & Disadvantages of Polymer Composites
Table of Contents
Polymer composites have evolved since the 1940s and play a significant role in modern-day products. Their applications to aircraft and other products have made their quality better and longer lasting. Composites polymers to hold the mixture together and various fibers as the reinforcement material.
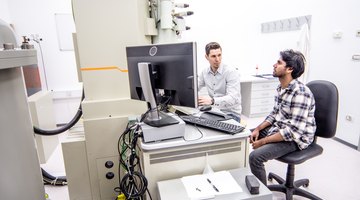
The origin of composites goes far back in history. The most common man-made composite was the combination of straw and mud to make bricks for construction. Another example is concrete, which combines cement and gravel. More recent composites use polymers as a resin or matrix to hold the mixture together and various fibers as the reinforcement material. These polymer composites have improved the performance of many modern-day products.
Matrix
The purpose of the matrix is to bind the fibers of the reinforcement together so that stresses are distributed throughout the material. The resin matrix also forms a hard surface that protects the reinforcement material from damage. Polymer matrix materials are two types: thermosets and thermoplastics. A thermoset matrix is created by an irreversible chemical-curing action of a resin to form an amorphous mixture. Thermosets have a high-temperature resistance, good resistance to solvents and high dimensional stability.
Thermoplastics are formed by heating to the process temperature and forming the product into the desired shape. They have a very high viscosity, making them more difficult to produce. Thermoplastics have more resistance to cracking and damage from impact as compared to thermoset composites.
Fibers
The role of fiber reinforcement is to add strength and stiffness to the combined material. Reinforcement comes in three forms: particles, continuous fiber and discontinuous fiber. Early reinforcement materials were straw, hemp and glass. In the 1940s, manufacturers began to combine carbon and glass fibers with polymer plastics to make a strong composite that could be used for aircraft hulls.
Strength
A significant advantage of polymer composites is their high tensile strength-to-weight ratio. Composites with polyaramid fibers are five times stronger than steel on a pound-for-pound basis. The fibers in these composites can be arranged during the manufacturing process in a multi-directional pattern that spreads stresses throughout the material. However, these materials have a low compressive strength, meaning they can break easily under sudden, sharp forces. A finished polymer composite will have a smooth surface, making it useful to reduce aerodynamic drag in aircraft.
Resilience
Polymer composites have excellent resistance to chemical corrosion, scratching, rust and seawater. These characteristics have led to applications in aircraft hulls, bicycle parts, military vehicles, trains and boats. Because of their durability to wear, low-cost composites have found uses in seats, walls and floors in buses and subways.
Costs
The cost of making polymer composites and forming them into useful products is the primary disadvantage. Polymer composites are manufactured by a laborious process known as lay-up that slows down production rates, making the products less cost-effective for high production volumes. Advanced polymer composites are likewise expensive to manufacture. These advanced formulas require more expensive training for labor and more sophisticated environmental and health considerations.
Polymer composites have continued to develop over the years with less costly manufacturing processes and better formulations with better strength and durability characteristics. As scientists learn more about the relationships between resins and reinforcement materials, the applications of polymer composites will continue to find more uses in everyday products. Stronger and lighter composites will find their way into more economical uses in transportation, boats and other products that were previously not thought possible.
References
Writer Bio
In 2007, Jim Woodruff began writing content for e-commerce Web sites and article directories. He specializes in business and finance. Woodruff holds a Bachelor of Mechanical Engineering from the Georgia Institute of Technology and a Master of Business Administration from the Columbia University Graduate School of Business.
More Articles