How Is High Density Foam Made?
Table of Contents
High-density foam, used for applications such as upholstery and shock absorption, is also called flexible polyurethane foam (FPF). According to the Polyurethane Foam Association, more than 1.7 billion pounds of high-density foam are manufactured annually in the United States.
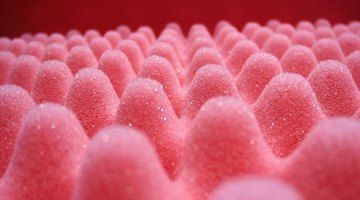
History
At the close of World War II, L.W. Schatz, founder of General Plastics Co., began experimenting with polyurethanes developed for wartime purposes. He noted that they were useful for surface coatings, sealants, shoe soles, small tires and other things. High-density foam resulted from polyurethane being combined with a blowing agent to create bubbles. The new material was highly touted as a replacement for cotton batting, thermal insulation and flotation devices.
Components
The two primary ingredients of high-density foam are polyol, typically a petroleum-based product, and di-isocyanate, a highly reactive chemical. Water and additives, such as flame-retardant additives, are also components of FPF.
Manufacturing Methods
As soon as the ingredients are mixed, bubbles form and expand the mixture, which rises similar to bread dough. The foam mixture is either poured onto a moving conveyor with sides to create slabstock, or it is injected into a mold. Slabstock is then further modified to the shape of the end product, such as a chair cushion, and molded foam is typically used for automotive or other commercial upholstery or for shock-absorbing packaging material.
Fire Safety
From its inception, FPF was acknowledged to be extremely flammable. FPF is more conducive to burning vigorously than other materials because of its expansive surface compared to its light weight, as well as its open-celled structure that allows oxygen into the pores to facilitate burning. Today, fire retardants are added to the mix. In addition, the fabrics used to cover high-density foam upholstery have a coated backing to further reduce flammability.
Alternative Ingredient
Biotechnology companies, such as Cargill, are involved in extracting greener polyols for foam manufacture. Increasingly more products are made from the company’s soy-based polyols. Testing has shown the soybean-oil foam matches the flexibility and density standards of traditional FPF. The alternative foam is no more biodegradable or less flammable than traditional foam, but at the end of its usefulness, it can be recycled.
References
Resources
Writer Bio
Jody C. Brown has worked as a freelance writer for the last 20 years. She has written and/or edited articles for Emory University and Thomson Publishing, as well as operated her own newsletter business for health professionals. Brown has a Bachelor of Arts in English from Valdosta State College.
Photo Credits
- pink foam image by laurent dambies from Fotolia.com
- pink foam image by laurent dambies from Fotolia.com
More Articles