How to Make Curved Carbon Composite Tubes
Composite tubing is specialized carbon fiber tubing used in industry, pharmaceuticals and plumbing. Its primary characteristics that attract users are its incredible strength-to-weight ratio and its resistance to most natural effects, like decay and mold. Composite tubing that is bent or curved is a specialized application of composites that supports complex applications and high-demand tube directions. The challenge in making curved composite tubes is the creation of a mold or mandrel, around which the composite fabric is wrapped. You can release and reuse this. You can best make one-inch curved composite carbon tubing around a copper tube surrounded with pipe insulation.
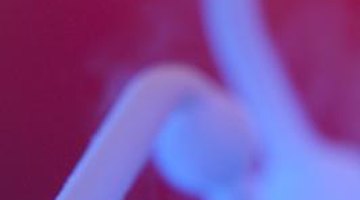
Step 1
Mark the required length of 1-inch copper tubing needed for the application using a tape measure. Cut the pipe to length with a reciprocating saw.
Step 2
Plug one end of the copper tubing using a 1-inch wood doweling piece. Stand the copper pipe vertically, standing on the plugged end, insert a funnel into the other end and fill the tubing with sand. Scrape out enough sand to allow you to plug the top end with another piece of dowel. You can now bend the sand-filled tube without kinking.
Step 3
Spray the exterior of the copper tubing with a liberal coat of vegetable cooking spray. Measure, cut and slide 1-inch pipe insulation around the copper pipe.
Step 4
Bend the copper tubing into a right angle or other angle shape as desired using a large steel pipe or similar fulcrum. Paint the pipe insulation with a liberal coat of epoxy resin release agent.
Step 5
Cut three strips of 2 x 2 carbon fiber fabric 3 1/2 inches wide and as long as the copper pipe using scissors. Mix the CF 862 epoxy resin and curing agent in a 3:1 ratio in a plastic bucket.
Step 6
Brush a light coat of epoxy release agent on the surface of the pipe insulation. Lay the first strip of carbon fiber fabric flat on a work surface and coat it generously with the epoxy resin mixture using a paint brush. Repeat this operation two more times for a three-layer stack of wetted fabric. You must also coat the top layer of fabric with the epoxy resin mixture.
Step 7
Wrap the wet fabric sandwich around the insulation-covered copper pipe. Wet your gloved hands with epoxy resin and slide them up and down the pipe with increased pressure to set and seal the fabric to the pipe. Allow the carbon fiber fabric to cure for 24 hours.
Step 8
Pull the copper tubing from the carbon fiber cylinder. Insert a length of mono-filament fishing line through the pipe and, working on the inside of the curve, pull the line back and forth to cut the pipe insulation and pull it out of the curved tubing.
References
Tips
- The flanges of the copper tubing cannot extend one inch beyond the end of the curve or the tubing will not slide out of the fabric cylinder.
Warnings
- Use caution when working with power tools.
- Wear gloves, goggles and breathing protection when working with epoxy resin.
Writer Bio
James Roberts began writing professionally in 1989, focusing initially on methodologies, multimedia courses and how-to articles on information technology, business, software, health care and relationships. His published works appear on various online article databases and he holds a Bachelor of Science in business from West Virginia University.
Photo Credits
- Hemera Technologies/AbleStock.com/Getty Images
More Articles