How to Install a Complete Compressed Air System
When building a compressed air system, it is common for many people to install an air compressor, wire it up, put a quick-disconnect hose fitting on it, then consider the project complete.
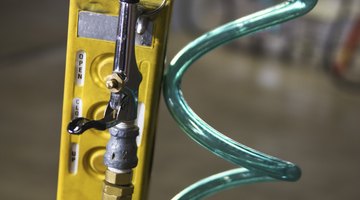
However, the presence of moisture, oil and dirt, any of which can ruin pneumatic tools and paint equipment, in such a setup must be addressed. This article will explain the necessary elements of a basic compressed air system and assist you in proper installation.
Tip
Always use hoses, pipes and fittings rated especially for high pressure compressed air applications. Ensure that you change your air filter's elements at the manufacturer-suggested intervals for maximum performance. Not all air dyers offer integrated drains. If the installation of an external drain is required, place it after the dryer and before the polishing filter.
-
Install the air compressor in a clean, dry, well ventilated room, at least two feet away from walls and corners. Sufficient space needs to be provided around the compressor for safe and proper inspection, cleaning and maintenance. Do not store toxic, volatile, or corrosive agents near the compressor or allow hot air from additional equipment to blow towards the compressor. Potentially hazardous noise levels should be taken into consideration as well. A separate compressor room is ideal. Electrical installation should be performed by a qualified electrician with knowledge of the National Electrical Code (NEC), OSHA code and/or any local or state codes having precedence.
-
Consider air treatment products. Connect an air hose or pipe from the compressor's discharge to a good quality coalescing or particulate filter. The purpose of a coalescing/particulate filter is to remove large particles (>1 micron) of oil, dust and other contaminants that are an unavoidable byproduct of the compression process.
-
Install a refrigerated air dryer. Connect your air hose or pipe from the filter's discharge to the dryer's inlet. The refrigerated air dryer will chill the compressed air to about +39°F. The lower compressed air temperature causes trapped water vapor to condense. The condensed moisture carries airborne dirt and oil to the moisture separator where it is removed from the system by an automatic drain. The relative low cost of a dryer can help save hundreds, even thousands of dollars in tool, equipment and application damage.
-
Install a polishing filter. Connect an air hose or pipe from the dryer's discharge to the polishing filter's inlet. The purpose of a polishing filter to remove microscopic (>.01 micron) particles of oil, dirt and liquid aerosols from the compressed air, ensuring the highest quality (non-medical) air possible.
The Drip Cap
- When building a compressed air system, it is common for many people to install an air compressor, wire it up, put a quick-disconnect hose fitting on it, then consider the project complete.
- A separate compressor room is ideal.
- The refrigerated air dryer will chill the compressed air to about +39°F.
- Install a polishing filter.
- The purpose of a polishing filter to remove microscopic (.01 micron) particles of oil, dirt and liquid aerosols from the compressed air, ensuring the highest quality (non-medical) air possible.
Writer Bio
This article was written by PocketSense staff. If you have any questions, please reach out to us on our contact us page.
Photo Credits
- Thinkstock/Comstock/Getty Images
- Thinkstock/Comstock/Getty Images
More Articles