How to Load Test a Generator
Part of the maintenance regimen for a generator is load testing.
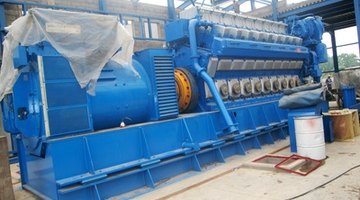
Placing a 100 percent capacity load on a generator and allowing it to run for awhile not only brings to light any problems in the generator and in the engine and its cooling system; it also benefits the engine by properly seating the rings and dislodging buildup in the combustion chambers and on the valves. Diesel engines especially need a periodic load test in order to maintain performance and fuel economy.
Things You Will Need
- Electric heaters and lights totalling 100 percent rated load
- VOM, true RMS
- Ammeter, clamp-on
-
Check all fluid levels in the generator. Make sure the fuel tank is full, the oil level is correct, and the radiator or coolant tank is full, if it is a water-cooled generator.
-
Start the generator and allow it to reach normal operating temperature. Watch and listen for any potential problems or abnormal noises. If any problems are noted, do not proceed with the test until you take care of them.
-
Begin connecting the loads, beginning with any large 220 volt loads and adding smaller 110 volt loads until each leg carries 50 percent of the maximum continuous rated load of the generator. Do not exceed 50 percent on any one leg. If possible, use 220 volt resistive loads, such as large space heaters or water heaters. They simplify this step because they apply the load to each leg equally.
-
Check the amperage of each leg with the ammeter, and check the voltage from each leg to neutral with the VOM set to read AC volts. For a 110/220 volt single phase generator, the voltage of each leg should fall between 105 and 125 volts, and the current should be half of the rated watt output divided by the voltage, for each leg. For example, if the voltage from each leg to neutral is 117 volts loaded, and the generator is rated at 10 kilowatts continuous, each leg should be loaded to 5000 divided by 117 or approximately 42 amperes. If one or both legs drops below 105 volts at full load, the generator has failed the test and needs repair.
-
Monitor the generator while maintaining this load for the duration of the test. Watch for overheating, listen for unusual noises, and monitor the output. If a problem develops, shut the generator down quickly to minimize damage, and repair the generator before returning it to service. How long the test should continue depends upon the type of generator. Light-duty portable generators should not be run at full load for more than three to four hours. Contractor grade generators should be able to run for eight hours. Continuous duty air or water cooled generators should run 24 hours. Larger industrial quality diesel generators should ideally be run under full load for about a week.
-
Remove the loads gradually at the conclusion of the test, and allow the generator to run under light load for one hour. Remove all loads five to ten minutes before shutting the generator down.
The Drip Cap
- Part of the maintenance regimen for a generator is load testing.
- Do not exceed 50 percent on any one leg.
- For a 110/220 volt single phase generator, the voltage of each leg should fall between 105 and 125 volts, and the current should be half of the rated watt output divided by the voltage, for each leg.
- If one or both legs drops below 105 volts at full load, the generator has failed the test and needs repair.
- Watch for overheating, listen for unusual noises, and monitor the output.
- Larger industrial quality diesel generators should ideally be run under full load for about a week.
References
- More Power To You! A Proven Path to Electric Energy Independence; H. Skip Thomsen; 1990
Writer Bio
Since 2008 Tracy Underwood has been fulfilling a lifelong dream of writing professionally. He has written articles for Possumliving.com and Woodsloafing.com online, and in print for "Backwoodsman Magazine." Underwood holds an Amateur Extra license from the FCC. He received an Electronic Technician certificate from the U.S. Navy BE/E school, NTC Great Lakes.
Photo Credits
- generateur1 image by JULIOPHOTO from Fotolia.com
- generateur1 image by JULIOPHOTO from Fotolia.com
More Articles