How to Oil a Key Wound Clock
When oiling a key-wound clock, it is necessary to remove the movement from the clock case according to specifications for the particular clock. The movement should also be thoroughly cleaned. The use of two different grades of clock oil designed to withstand different degrees of torque or power within the movement gear train should be used. Mainspring gears in a key-wound clock unwind slowly, as do the gears closest to them, requiring a higher viscosity oil that resists flowing. But as the power transfers from gear to gear, the torque is reduced and the gears travel at a quicker pace where a thinner oil should be used. A clock owner can oil their key-wound movement in 30 minutes or less with a few tools and materials.
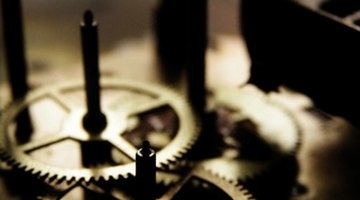
-
Remove the torque from the clock mainspring by inserting the proper-sized end of the mainspring let-down tool over the winding arbor and twisting the let-down tool as if to wind the spring until pressure on the mainspring ratchet wheel pawl lever, also known as a click, is relieved.
-
Lift and hold the pawl lever above the teeth of the ratchet wheel with the tweezers and slowly release the hand-grip pressure on the mainspring let-down tool allowing the mainspring to slowly unwind. In lieu of this special mainspring tool, the torque can be relieved by allowing the clock to completely run down. Do the same for all additional mainsprings the clock movement may have, such as striking mechanism springs and chime mechanism springs
-
Lubricate the mainspring coils with small amounts of approved mainspring grease. The grease can be applied using a flat tooth pick. In lieu of clock grease, apply one drop of high viscosity synthetic clock oil on each coil.
-
Apply one drop of clock oil into each oil sink on the outside of the movement plates. Wipe any excess off the plates using a clean cotton cloth. Use high viscosity oil in the lower oil sinks and lower viscosity oil on the middle to upper oil sinks of the movement.
-
Apply one small drop of low viscosity oil to the tip of one of the escape wheel teeth. The oil drop will be distributed across the steel pallet surfaces of the escapement verge as the clock is in motion.
-
Lubricate all strike and chime lever pivots in the front of the movement with one drop each of high viscosity oil. Chime mechanism pivots in the rear of the clock movement should be lubricated with one drop each of high viscosity oil.
References
Tips
- Other than placing a small drop on one tooth of the escape wheel, the brass gears of the movement do not require any lubrication. The steel pinions that the brass gears engage and are meshed with do not require any lubrication.
Warnings
- Never use penetrating oils such as WD-40 to lubricate a clock movement. Use only approved synthetic clock oils and grease.
- Do not attempt to use a clock key to unwind a mainspring. Serious injury can occur to hand and fingers as well as damage to the clock movement. Use proper mainspring let-down tools or allow the clock to wind completely down on its own.
Writer Bio
Max Stout began writing in 2000 and started focusing primarily on non-fiction articles in 2008. Now retired, Stout writes technical articles with a focus on home improvement and maintenance. Previously, he has worked in the vocational trades such as automotive, home construction, residential plumbing and electric, and industrial wire and cable. Max also earned a degree of biblical metaphysician from Trinity Seminars Ministry Academy.
Photo Credits
- clock mechanism image by Pali A from Fotolia.com
More Articles