How to Troubleshoot a Ryobi Two-Stroke Engine
A majority of Ryobi’s line of power tools use a two-stroke gas-powered engine. These engines, with their simplicity and efficiency, only require three basic things to run: spark, gas and compression. Almost all of the parts of the engine relate to one of these three systems.
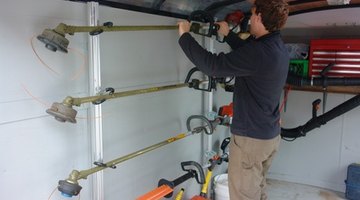
If a part in a particular system breaks down, other parts in the same system usually follow. That’s why it’s best to troubleshoot your problems into one of these areas before attempting to fix one part, which may only be a symptom of a larger problem.
Troubleshooting A Bad or No Spark
-
Lift off the spark plug’s rubber boot. Use the socket wrench to remove the spark plug. Check the inside of the rubber plug for any dirt or oil buildup.
-
Put a new spark plug into the rubber boot. Hold the rubber cable, using leather gloves, near a metal spot on the engine block. Tug on the starter cord a few times and look for a blue spark across the points. If there’s no spark or it’s weak, replace spark plug and try it again.
-
Inspect the rubber plug and wire for any damaged or loose connections. Use the screwdriver to remove the ignition module from the handle. Check for any damaged or loose wires and that the “ON/OFF” switch is properly working.
-
Take the machine to a mechanic to have him test the starter coil and magneto gap for a charge. You should also have him make sure the electrical wiring for the ignition module is grounded before replacing a starter coil or starter.
Troubleshooting Compression Problems
-
Pull the starter cord. It should be neither too hard nor too easy to pull out. If it is, you compression is low. Start the engine, if you can, and tune the carburetor.
-
Remove the air filter cover and muffler cover with the screwdriver. Take off the air filter and pull out the spark arrestor screen from the muffler. Wash both of these in warm, soapy water with a metal brush. Replace if they’re too dirty to clean. Put them back in the engine.
-
Inspect the muffler’s exhaust port for any clogs or heavy carbon buildup. Clean if necessary. Make sure the muffler is properly attached to the engine and dispensing the exhaust properly.
-
Check the piston seals, rings and gaskets inside the engine. Replace if they’re loose or worn out. Check the piston, bore and cylinder for any cracks, which could be causing any compression loss.
-
Take it to a mechanic to have him test the engine for compression and leaks. Most small engines will need about 90 psi to operate correctly.
Troubleshooting Gas-Related Problems
-
Empty out any old gas before trying to restart the engine if it has been stored for over one month. Check the fuel tank for any dirt or debris that could be choking the carburetor of gas. Clean the tank with a rag and brush if necessary.
-
Inspect the fuel filter and fuel line for any damage or clogs. Disconnect the fuel line and tip the engine upside down to see if gas is reaching the carburetor. If it’s not reaching the carburetor, replace the fuel filter and fuel line.
-
Disconnect the carburetor from the engine. Dismantle it and clean every part in a carburetor cleaner bath. Let them soak overnight. Scrub each part clean with the wire brush.
-
Check all of the screens and filters. Make sure the diaphragm isn’t warped or otherwise damaged. Check for any hidden clogs in the needle valve. Reassemble carburetor with a carb kit.
-
Take the engine to a mechanic to check the crankcase and crankshaft. Replace carburetor if necessary.
Things You Will Need
- Socket wrench
- Screwdriver
- New spark plug
- Rag
- Brush
- Carburetor cleaner
- Carb kit
References
Writer Bio
Currently based in Minneapolis, Minn., Eric Blankenburg has been a freelance journalist since 2000. His articles have appeared in "Outside Missoula, Outside Bozeman," "Hello Chengdu" and online at GoNomad.com and various other websites. He holds a Bachelor of Arts in creative writing from the University of Montana.
Photo Credits
- line trimmers image by Horticulture from Fotolia.com
- line trimmers image by Horticulture from Fotolia.com
More Articles