Homemade Concrete Pool Table
Building a pool table from a weatherproof material such as concrete enables you to enjoy a game of pool outside, regardless of the weather. Casting a homemade pool table is a monumental task, requiring several days of labor, but in the end you’ll have a unique and permanent addition to your backyard.
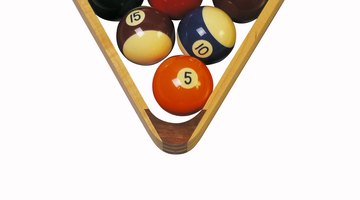
Forming the Legs
The surface of a regulation pool table is eight feet long and four feet wide. The density of concrete means your finished pool table will weigh around 2,000 pounds. Plan to pour your table in place on an existing slab or on concrete piers to keep it from sinking into the soil over time. Wide table legs spread the weight over a greater area. Plan at least four legs for the table, each one foot square. Build molds from 3/4-inch particleboard coated with melamine or use 12-inch circular fiber concrete molds. Make the molds at least 28 inches tall and space them in a 3-by-7-foot rectangle. Mix your own concrete or hire a commercial cement mixer to pour the legs. You’ll need about 840 pounds of dry concrete mix. Add two quarts of Portland cement for each bag for stronger concrete. Let the legs cure at least 48 hours. Do not yet remove the forms.
Pouring the Surface
The surface of your pool table will be cast like a wide, two-inch thick concrete counter top. Build a mold out of melamine particleboard and support it with sawhorses. Fit the mold so the concrete will connect directly to the previously cast legs. Use metal garden edging to form the “mouths” of the six pockets. It’s simpler to build your mold to cast only the playing surface and construct the side rails from wood after the concrete cures, though the rails can also be cast at the same time. In the center of the mold, construct a rebar lattice or use a wire agricultural panel for reinforcement. The play area requires around 780 pounds of dry concrete mix. Pour the concrete and vibrate the mold with a blade-less reciprocating saw for a smooth finish. Let the table cure for two hours and smooth the surface with a trowel. Cover with plastic and let it cure for 48 hours.
Pool Table Finishing
Remove the forms and power-sand the surface with 180-grit sandpaper. Finish the table with a stretched, pre-cut waterproof tablecloth over the concrete surface. Attach regulation rubber cushions to the side rails and weather-resistant pockets to catch the pool balls. While your table and pool balls will withstand the elements, store pool cues indoors.
The Drip Cap
- Building a pool table from a weatherproof material such as concrete enables you to enjoy a game of pool outside, regardless of the weather.
- You’ll need about 840 pounds of dry concrete mix.
- Let the legs cure at least 48 hours.
- It’s simpler to build your mold to cast only the playing surface and construct the side rails from wood after the concrete cures, though the rails can also be cast at the same time.
- In the center of the mold, construct a rebar lattice or use a wire agricultural panel for reinforcement.
- Remove the forms and power-sand the surface with 180-grit sandpaper.
References
Writer Bio
Based in Colorado, Erik Johnson has been writing professionally since 1996 and has worked in real estate, management and technical fields. Recipient of the 3M Richard G. Drew Recognition of Creativity, Johnson is the author of three books.
Photo Credits
- Comstock/Comstock/Getty Images
- Comstock/Comstock/Getty Images
More Articles