How to Zero a Dial Caliper
A dial caliper is a measuring instrument with an accuracy rivaling that of a micrometer. Both devices can measure to the nearest thousandth of an inch. The advantage of a caliper is that you can measure up to several inches in length with having a whole set of them as would be necessary with micrometers.
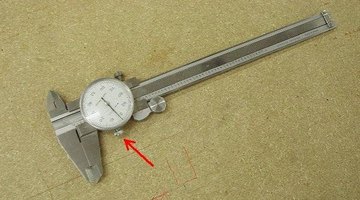
The slightest bit of wear on the moving parts of the dial can throw off the accuracy of the zero setting. Fortunately, a provision is made so that you can easily adjust the zero on your dial caliper.
-
Be sure that there are no dust or dirt particles between the jaws of the caliper.
-
Turn the thumb wheel of the caliper until the jaws are completely closed.
-
Loosen the adjustment lock screw. On this particular caliper (see photo), the screw is pointed out by a red arrow.
-
Turn the dial until the the hairline indicator (the hand on the dial) is on the zero. It doesn't matter how the orientation of the dial is set.
-
Tighten the adjustment lock screw. Your caliper will now read correctly when you take a measurement.
The Drip Cap
- A dial caliper is a measuring instrument with an accuracy rivaling that of a micrometer.
- Loosen the adjustment lock screw.
- Your caliper will now read correctly when you take a measurement.
Writer Bio
Gene Tencza has worked in the furniture industry all his life. Tencza has always been a chronic home handyman, mechanic and "Jack of all trades". He has been writing professionally for eHow.com since May of 2009. Tencza has a Bachelor of Science in industrial education from Central Conneticut State University
Photo Credits
- Photo by Gene Tencza
- Photo by Gene Tencza
More Articles