How to Grease Mower Spindles
Mower spindles house a small shaft that transfers mechanical energy between the lawnmower belt and the mower blades. The spindles bolt to the mower deck and support the belt pulleys on the top and connect to the mower blades on the bottom, beneath the deck.
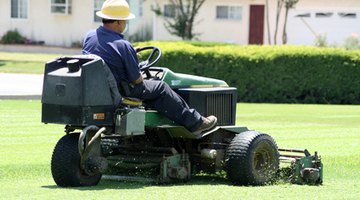
Each spindle includes two bearings contained in a single cavity. The spindle shaft runs through the bearings at the top and the bottom of the spindle housing. In order to maintain the mower spindles in good working order, grease the bearings at least twice during a mowing season.
-
Operate the mower deck for up to five minutes to warm and soften the existing grease inside the mower spindles.
-
Park the mower and set the parking brake.
-
Lower the mower deck to its lowest setting using the deck adjustment lever on the lawn mower. The grease fittings mount to the spindles just above the mower deck. Lowering the deck from the mower allows more access to the spindles for servicing.
-
Spray each grease fitting with a light coat of machine oil and wipe each fitting clean with a lint-free shop rag. Removing the dirt from the fitting allows the fresh grease to flow unrestricted through the fittings and into the spindle housings.
-
Press the grease gun coupling onto each fitting and pump the gun handle three to four times. If more than a year has passed since the last time the spindles were greased, double the pumps of grease to six or more.
-
Wipe extra grease from the grease fittings with the rag after each spindle has been greased.
-
Start the lawn mower and run the mower deck for five or six minutes to disperse the grease within the spindles.
Things You Will Need
- Machine oil
- Lint-free rag
- Grease gun
Tip
Clean the mower deck after each mowing session to help preserve the mower spindles and bearings.
Warning
Remove the keys from the mower while servicing the mower deck to avoid accidental starts.
References
Writer Bio
Damon Hildebrand is a retired U.S. Navy veteran. He has more than 15 years within the oil and gas industry in both technical and managerial positions. Hildebrand has been a technical writer and communicator for the last four years. He is a certified specialists in lubrication and tribology, as well as a certified maintenance and reliability professional.
Photo Credits
- Man mowing image by xymm from Fotolia.com
- Man mowing image by xymm from Fotolia.com
More Articles