How to Hook Up a PID SSR & Heating Element
Using a PID controller with a built-in solid state relay to control a heating element allows a responsive heating system that can be set up to reach and maintain a temperature set-point in the most efficient manner.
The P, I and D in PID controller stand for Proportional, Integral and Derivative. These are coefficient values that can be set inside the PID control to determine how responsive the system is to "error" or the difference between set-point and actual temperature.
An SSR, or Solid State Relay is the switch that turns the heater on and off as the controller requires. It can respond quickly to the PID controllers demands. As it's name implies, The SSR is a solid state device, meaning it has no moving parts that can wear out.
This article assumes that you have already mounted the PID controller inside a control panel and have multiple AC power connections available (hot, neutral, ground).
Wiring a PID controller with built-in SSR to a heating element.
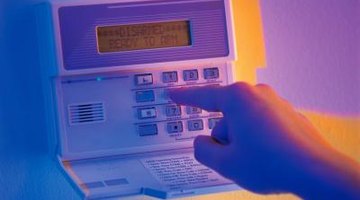
Step 1
Connect AC power wires (Hot, Neutral and Earth Ground) to the PID Controller.
Step 2
Connect AC hot wire (typically a black wire) to the Load terminal of the PID controllers SSR output.
Step 3
Connect a black wire from the other Load terminal of the SSR output to the heater.
Step 4
Connect a Neutral (white) wire to the other heater element terminal and wire this to a neutral connection inside the control panel.
Step 5
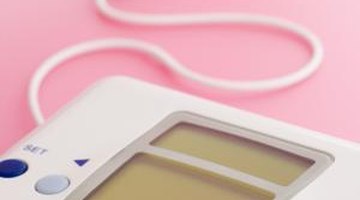
Connect the Thermocouple (Temperature probe to the SSR PID control, if applicable). There will be a + and - indication on the terminals where it is to be wired into the controller. These connections will be for the very light wire gauge of thermocouple wire.
Step 6
Power on the controller.
Step 7
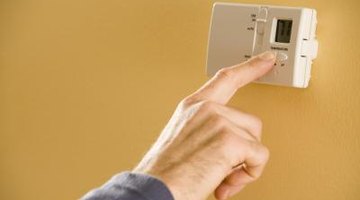
Enter the temperature set point into the SSR PID heating controller.
Step 8
Enter in a value for P, Proportional.
The Proportional value makes a change in the control's output that is in the same amount as the difference between set-point temperature and actual temperature. The number entered for this gives a "weight" or severity to the impact of the proportional value.
Since every heating control system will have a different thermal mass, it is impossible to give a standard exact value that will work in every instance.. Start with any arbitrary value. If the systems respond too quickly and tend to overshoot the temperature set-point, decrease this value. If the system responds too slowly, taking a long time to reach the set-point, increase this value.
Step 9
Enter in a value for I, (Integral).
The integral value takes into account the absolute value of the error between set-point and current process value, as well as the amount of time that the value has been below or above the set-point.
As with proportional, the integral value is different for every system and is a matter of playing with numbers until you find a value that works. Start with 1/2 the value used for proportional and adjusting up or down until you find a value that causes the system to respond as quickly as possible and with a minimal temperature overshoot.
Step 10
Enter in a value for D (Derivative).
The derivative value compensates for the slope of the error over time. It is often referred to as the "look ahead" value.
The derivative value helps to smooth the response of the system, knocking down the amount of temperature overshoot. This comes at the cost of slowing down the overall response of the system.
Unless the system you are setting up tends to experience a large degree of overshoot, leave this value very low. Even zero it out if you are getting acceptable system response times by just playing with the P and I values.
Step 11
Keep testing PID loop values until you get the desired response. Doubling values and cutting values in half is the best way to quickly find what works.
References
Resources
Tips
- It can be tricky to program a PID control. If you have problems getting the loop to control properly, play with ONLY the P and I values and ignore or zero out the derivative value.
Warnings
- If the PID controller does not have an internal fuse between the SSR and the heating element, to add one, or make sure power is run through a circuit breaker.
- In a system where the demands are dynamic, for example temperature set-points that change dramatically, be on the lookout for system oscillation. This can occur if P and I values are too high. Test out a system over the intended ranges of set-points to ensure that the PID loop values do not make the system unstable.
- Do not cut or splice thermocouple wires. Altering them will change their resistance and make the temperature control read incorrectly.
Writer Bio
James Miller is an Electrical Engineer who has experience in OEM electronic equipment and PLC programming. As a sideline he dabbles in real-estate investing, Web development and programming. He writes instructional articles for various websites.
Photo Credits
- Comstock/Comstock/Getty Images
- BananaStock/BananaStock/Getty Images
- Comstock Images/Comstock/Getty Images
More Articles