DIY Hydrostatic Drive
Hydrostatic drive has become increasingly popular as a transmission strategy for a variety of utility vehicles. It is used in every lawn tractor sold in the 2000s because of the almost infinite variability of its output speed. Because hydraulic hoses are easily flexed in normal operation, it is much easier to build vehicles that do not require shaft couplings to get rotational force to go around corners. Hydrostatic transmissions make it easy to build unique-wheeled vehicles such as a rugged outdoor wheelchair.
Hydrostatic Characteristics
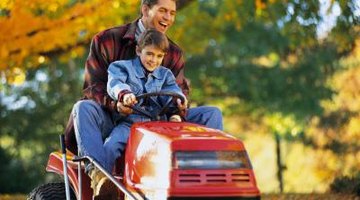
Like gear transmissions, hydrostatic drives deliver higher torque to the wheels proportionately to the decrease in speed. They can continuously vary speed and output torque to exactly the value the operator wants. They are used mostly in low-speed applications.
Hydrostatic Wheelchair Drive
Zero-turn lawn mowers use a gasoline engine to drive a hydraulic pump. The hydraulic oil is routed through two control valves, each of which controls a hydraulic motor that has a wheel hub mounted to it. The pump’s output drives low-speed, high-torque hydraulic motors. The valves are both reversible and their internals shaped such that the flow to each motor can be deftly regulated. Zero-turn vehicles use the difference between widely spaced tractor tires to turn the vehicle and propel it forward or backward. A hydraulically driven vehicle can be very carefully controlled and they do go precisely where they are steered despite the terrain. Many say the most difficult part of the wheelchair existence is what people can no longer do -- take a stroll though a field, walk their dogs or cross rugged terrain. The hydrostatic drive wheelchair enables wheelchair adventurers to resume the rigorous outdoor agendas they once enjoyed. It is an excellent hydrostatic application.
Drive Strategy
This vehicle uses the same drive strategy as the zero-turn lawn mower, less the mowing. A 4-horsepower vertical shaft lawnmower engine turns the 11-gallon-per minute pump via a 3-to-1 reduction belt drive. A small reservoir holds the hydraulic oil, and an inline filter before the pump keeps the system clean and running. A control lever valve is mounted in front of each arm. The motors drive and hold the large, aggressive drive wheels. They enable the driver to go forward, backward, and take any turn to tight circles -- wherever they want to do it!
Build Strategy
Visit a chain hardware store and study the zero-turn mowers, noting scale and proportions. A sturdy pedestal, captain’s-style boat seat with arms can be used for functional comfort. The seat should be centered right in front of the large independent drive wheels. Front wheels should be substantial pneumatic-tired swivel wheels. They should be at least four feet in front of the rear drive wheels, and spaced at 42 inches, like the drive wheels, for stability. The seat should be no higher than 16 inches off the deck to keep the center of gravity low. The frame should be constructed from welded two-inch square steel tubing. No brakes are required because when the control levers are released, the hydraulic motors lock.
Downside
The most difficult aspect of this project is getting the ecstatic user off it at night!
References
Writer Bio
Pauline Gill is a retired teacher with more than 25 years of experience teaching English to high school students. She holds a bachelor's degree in language arts and a Master of Education degree. Gill is also an award-winning fiction author.
Photo Credits
- Comstock/Comstock/Getty Images
More Articles