How to Remove the Impeller on a Hot Tub Pump
Hot tub motors power the circulation of the tub's small body of water. The water circulation stems from an impeller inside the hot tub pump. The pump impeller sits threaded on a motor shaft, which spins at high speeds when the pump is in operation. The spinning of the impeller pulls and pushes the water throughout the hot tub system using centrifugal force. Remove the impeller on a hot tub pump requires breaking down the pump to gain access to the impeller and motor shaft.
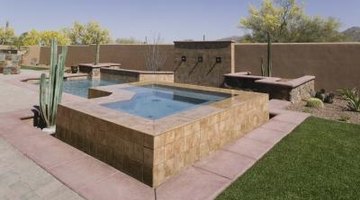
-
Turn off the hot tub and open its access panel. Disconnect the pump from the spa plumbing. If no unions or quick disconnect fittings exist on the plumbing, use a PVC hacksaw to free the hot tub pump.
-
Unbolt the bolts placed on the housing of the hot tub pump using a wrench. Pull the housing away from the motor of the hot tub pump to expose the motor shaft, impeller and diffuser.
-
Unscrew the screws holding the diffuser to the motor using a screwdriver or pliers. Pull the diffuser away from the motor section.
-
Unscrew the screw seated into the center of the hot tub impeller with a screw driver. Impeller screws can be backwards threaded, so take care not to strip the screw when removing it.
-
Latch a wrench or pliers onto the hot tub motor's shaft behind the impeller. If the motor shaft behind the impeller is not easily accessible, remove the pump's back casing to gain access to the shaft.
-
Rotate the impeller off the shaft threads while preventing any movement in the shaft with the wrench or pliers. Pull the impeller off the shaft once its off the shaft threads.
References
Tips
- Regularly inspect the impeller and seal of your hot tub pump monthly to prolong the life of the pump.
Writer Bio
Justin A. Mann has been a freelance writer since 2007. Mann is experienced with computers and all things relating to swimming pools, and he uses his knowledge in these fields to write articles for various websites. Mann is an English major at East Central University.
Photo Credits
- Jupiterimages/Comstock/Getty Images
More Articles
- How to Clean The Pump Filter on a GE Front Loading Washing Machine
- How to Disassemble an AC Fan Motor
- How to Troubleshoot a Campbell Hausfeld High Pressure Washer
- How to Remove a Corroded Old Bathtub Drain
- How to Change the Belt for a Kenmore Dryer Model 110
- How to Replace the Belt on a Whirlpool Washer